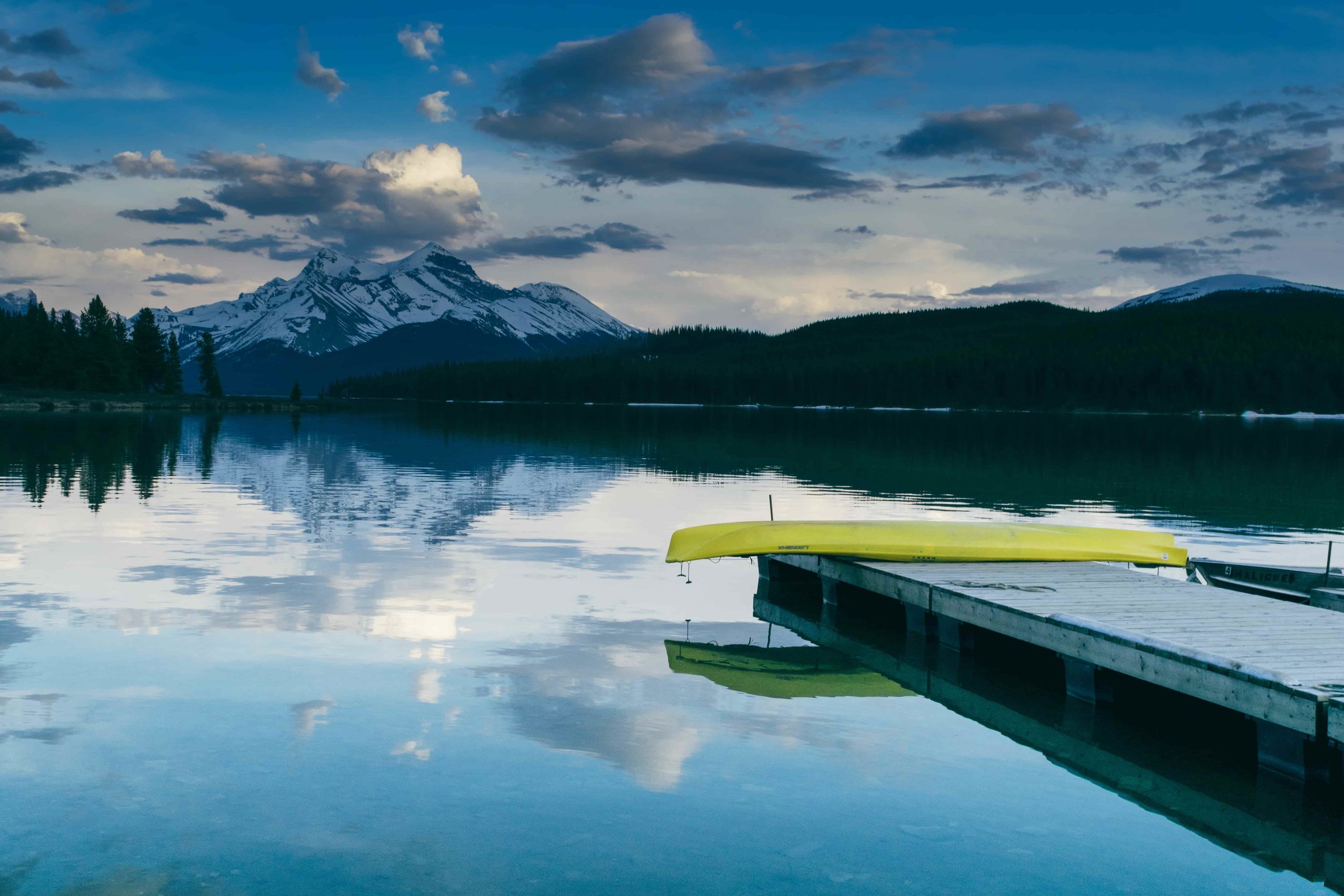
LE BLOG DE LA CHAÎNE D'APPROVISIONNEMENT
Optimisation des entrepôts : Maximiser l'utilisation de l'espace et réduire les coûts
Dans le monde du management de la chaîne d'approvisionnement, les entrepôts jouent un rôle crucial dans le stockage et la distribution efficaces des marchandises. Cependant, de nombreuses entreprises sont confrontées à un manque d'espace et à des coûts opérationnels croissants, ce qui peut nuire à la productivité et à la rentabilité. La clé pour surmonter ces défis réside dans l'optimisation des entrepôts. En maximisant l'utilisation de l'espace et en réduisant les coûts, les entreprises peuvent dégager des avantages significatifs et acquérir un avantage concurrentiel sur le marché. Dans cet article, nous allons explorer des stratégies pratiques et des conseils concrets pour optimiser vos opérations d'entreposage et tirer le meilleur parti de votre entrepôt ou de votre centre de distribution.
Dans le monde du management de la chaîne d'approvisionnement, les entrepôts jouent un rôle crucial dans le stockage et la distribution efficaces des marchandises. Cependant, de nombreuses entreprises sont confrontées à un manque d'espace et à des coûts opérationnels croissants, ce qui peut nuire à la productivité et à la rentabilité. La clé pour surmonter ces défis réside dans l'optimisation des entrepôts. En maximisant l'utilisation de l'espace et en réduisant les coûts, les entreprises peuvent dégager des avantages significatifs et acquérir un avantage concurrentiel sur le marché. Dans cet article, nous allons explorer des stratégies pratiques et des conseils concrets pour optimiser vos opérations d'entreposage et tirer le meilleur parti de votre entrepôt ou de votre centre de distribution.
Réaliser une analyse complète de l'agencement de l'entrepôt : Une étape cruciale de l'optimisation de l'entrepôt consiste à analyser l'agencement actuel afin d'identifier les inefficacités et les domaines susceptibles d'être améliorés. Prenez en compte des facteurs tels que la densité de stockage, le flux de produits, l'accessibilité et la sécurité. L'évaluation critique de l'agencement de votre entrepôt vous permettra d'identifier les possibilités de réorganiser les zones de stockage, d'améliorer la configuration des allées et d'utiliser efficacement l'espace vertical.
Adopter la technologie et l'automatisation : L'intégration de la technologie et des solutions d'automatisation peut révolutionner les opérations de votre entrepôt. La mise en œuvre du bon système de gestion d'entrepôt (WMS) peut rationaliser le contrôle des stocks et l'exécution des commandes, améliorer la précision globale et permettre d'autres améliorations. En outre, des technologies telles que la lecture de codes-barres, l'étiquetage RFID et les systèmes automatisés peuvent améliorer les processus de préparation et d'emballage, réduire les erreurs humaines et faire gagner un temps précieux.
Donner la priorité à la gestion des stocks et à la planification des ventes et des opérations (S&OP) : il est très important d'envisager la planification de la chaîne d'approvisionnement d'un point de vue holistique, de bout en bout. Cela aidera l'ensemble de l'entreprise sur le plan stratégique et aura un impact positif sur le fonctionnement de l'entrepôt grâce à une meilleure gestion des stocks. La réussite du S&OP et de la gestion des stocks est cruciale pour l'optimisation de l'espace et la réduction des coûts. En comprenant les niveaux de stock, les taux de rotation et les modèles de demande, il est possible de mettre en œuvre des stratégies qui minimisent les stocks excédentaires, réduisent les coûts de possession et maximisent l'espace disponible. En outre, l'adoption d'une méthode d'analyse ABC permet de hiérarchiser les articles en fonction de leur valeur et d'optimiser l'affectation des espaces de stockage en conséquence.
Mettre en œuvre les principes du Lean : L'application des principes du Lean aux opérations d'entreposage peut conduire à des améliorations significatives en matière d'utilisation de l'espace et de réduction des coûts. Des techniques telles que les 5S (Trier, Mettre en ordre, Briller, Standardiser, Maintenir) peuvent améliorer l'efficacité des postes de travail en éliminant les déchets et en créant un espace de travail organisé et efficace. Les méthodologies "lean" favorisent également l'implication des employés, créant ainsi une culture d'amélioration continue.
Optimiser les stratégies de slotting et de picking : Des stratégies efficaces de slotting et de picking peuvent minimiser les temps de déplacement, réduire les coûts de main-d'œuvre et améliorer la productivité globale de l'entrepôt. Analysez la vélocité de vos UGS et les schémas de commande pour placer stratégiquement les articles à rotation rapide plus près des zones d'expédition, réduisant ainsi le temps nécessaire au prélèvement et à l'emballage des produits très demandés. Révisez et ajustez régulièrement vos stratégies de slotting pour les adapter à l'évolution de la demande et des besoins de l'entreprise.
Favoriser la collaboration avec les fournisseurs : Une collaboration étroite avec les fournisseurs peut contribuer à optimiser les opérations d'entreposage et à réduire les coûts. Explorez les programmes de gestion des stocks par le fournisseur (VMI) qui permettent aux fournisseurs de contrôler et de réapprovisionner directement les niveaux de stock. Cela permet de réduire les délais, de minimiser les ruptures de stock et de libérer de l'espace dans l'entrepôt. En outre, étudiez les possibilités de modifier la façon dont les fournisseurs expédient les produits afin d'accélérer les processus de réception et d'entreposage. Parmi les changements possibles, citons l'emballage, les étiquettes et les pratiques de transbordement pour réduire la manutention.
L'optimisation des entrepôts est un aspect essentiel de la gestion de la chaîne d'approvisionnement qui peut apporter des avantages significatifs aux entreprises. En maximisant l'utilisation de l'espace, en mettant en œuvre des processus efficaces et en tirant parti de la technologie, les entreprises peuvent réduire leurs coûts, améliorer leur productivité et accroître la satisfaction de leurs clients. N'oubliez pas que l'optimisation de votre entrepôt est un processus continu qui nécessite une surveillance, une analyse et une adaptation permanentes à l'évolution de la dynamique du marché. En adoptant les stratégies présentées dans cet article de blog, vous pouvez adopter une approche proactive de l'optimisation de votre entrepôt, libérer tout son potentiel et positionner votre entreprise sur la voie de la réussite dans le paysage concurrentiel du marché.
Introduction au prélèvement par commande vocale (VDP)
La technologie de prélèvement vocal est un équipement qui permet d'avoir les mains et les yeux libres dans l'entrepôt. Elle devient actuellement une nouvelle norme dans les centres de distribution, utilisée principalement pour les opérations de sortie, mais peut être appliquée à n'importe quel processus dans un entrepôt. En effet, pour les opérations sortantes, la préparation de commandes à commande vocale (VDP) augmente la productivité globale, la précision et la sécurité dans l'installation.
Qu'est-ce que le Voice Picking ?
La technologie de prélèvement vocal est un équipement qui permet d'avoir les mains et les yeux libres dans l'entrepôt. Elle devient actuellement une nouvelle norme dans les centres de distribution, utilisée principalement pour les opérations de sortie, mais peut être appliquée à n'importe quel processus dans un entrepôt. En effet, pour les opérations sortantes, la préparation de commandes à commande vocale (VDP) augmente la productivité globale, la précision et la sécurité dans l'installation.
VDP adapte la technologie Bluetooth et s'intègre au système WMS ou ERP de l'entrepôt. Au lieu qu'un employé lise des informations sur une liste de prélèvement ou un scanner, le système communique avec l'employé via un casque sans fil et lui indique où aller dans l'entrepôt et ce qu'il doit prélever. Le VDP fournit également une confirmation en temps réel, supprimant la nécessité de scanner physiquement et d'enregistrer les informations, ce qui améliore l'efficacité.
Quels sont les avantages ?
Réduire les erreurs de prélèvement et accroître la sécurité
Comme nous l'avons mentionné, le VDP crée un environnement "mains libres". Il n'est plus nécessaire d'appuyer sur des boutons, d'enregistrer/interpréter manuellement des informations, etc. Au lieu de cela, l'employé qui porte le casque suit les instructions données par les commandes vocales et le retour d'information audio, qui sont directement enregistrés dans le système WMS. La facilité d'utilisation du VDP permet de réduire le nombre d'erreurs de prélèvement qui seraient normalement dues à des erreurs humaines.
La sécurité dans l'entrepôt est l'élément le plus important de toute installation. De nombreux facteurs doivent être pris en compte, tels que les équipements de manutention et les autres employés présents sur le sol, qui peuvent provoquer des accidents indésirables. La capacité de VDP permet aux employés d'être plus conscients de leur environnement lorsqu'ils se déplacent dans l'entrepôt. Ils ne sont plus distraits par la lecture de leur liste de prélèvement ou de leur scanner dans l'entrepôt et n'ont plus qu'à se concentrer sur leur déplacement en toute sécurité jusqu'à leur lieu de prélèvement.
Productivité accrue
Selon Körber Supply Chain, l'intégration du VDP dans l'entrepôt se traduit généralement par une augmentation de 20 à 25 % de la productivité. L'intégration élimine immédiatement le besoin de papier supplémentaire et d'appareils portables, ce qui réduit le temps nécessaire pour s'arrêter, lire et scanner les articles et les listes de sélection. Au lieu de cela, l'écoute et la parole permettent à l'utilisateur d'effectuer plusieurs tâches pendant la procédure de prélèvement. Ensuite, au fur et à mesure que les données sont collectées, il est possible d'accroître encore la productivité en trouvant l'itinéraire de prélèvement le plus optimal. Ces informations peuvent être extraites pour réduire le temps de déplacement dans l'entrepôt. Ces gains de productivité réduisent la main-d'œuvre nécessaire à la préparation des commandes, ce qui permet de réaffecter les ressources là où elles sont nécessaires.
Le VDP est également intégré aux robots de préparation des commandes afin d'accroître encore la productivité. En plus de l'utilisation du PDV par un employé, les robots de préparation de commandes utilisent le temps moyen de préparation et de déplacement pour s'assurer que le préparateur et le robot sont juste à temps l'un par rapport à l'autre. Ces robots constituent un élément supplémentaire dans le processus d'automatisation.
Données et amélioration continue
Cette méthode permet non seulement de fournir des informations en temps réel, mais aussi de collecter des données afin d'obtenir des statistiques utiles, telles que la durée de la tâche et le nombre moyen d'articles sur la liste de prélèvement. Ces statistiques sont importantes pour l'amélioration continue de l'entrepôt. L'accès à ces informations permet de s'assurer que les préparateurs de commandes arrivent à temps, au bon endroit et, à plus grande échelle, de maintenir les indicateurs de performance clés.
L'avenir du PDV
Alors que les entrepôts continuent d'introduire de nouvelles technologies, l'utilisation du VDP va continuer à se développer car il augmente la précision sans sacrifier le temps. L'intégration avec les robots de préparation de commandes se développera très probablement en parallèle en raison de leurs fonctionnalités complémentaires, ce qui renforcera encore les normes. La liberté qu'offre le VDP permet à une entreprise de s'attaquer à d'autres goulets d'étranglement dans l'entrepôt, tels que l'assurance qualité ou le stockage des stocks, en réaffectant la main-d'œuvre de préparation des commandes là où elle est nécessaire. Non seulement la productivité augmente dans l'entrepôt, mais le PDV permet également aux entreprises de s'appuyer davantage sur les données, ce qui est essentiel pour une croissance et une amélioration continues.